XK-ME1 PHOTE-ELECTRO-MECHANICAL INTEGRATION TRAINING SYSTEM
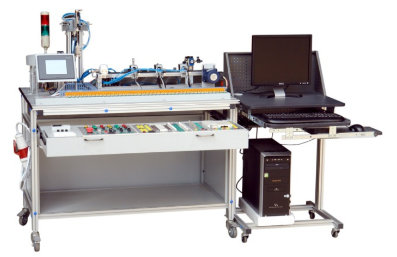
PRODUCT INTRODUCTION XK-ME1consists of aluminum alloy guide rail type training platform, feeding mechanism, feeding material testing mechanism, carrying mechanism, material delivery and sorting mechanism, etc. Mechanisms are closely connected, students are freely to assemble and debugging. XK-ME21 control system adopts modules combination type, it consists of touching screen module, PLC module, inverter module, button module, power source module, wiring terminal strip and kinds of sensors. The touching screen module, PLC module, inverter module, button module are required to combine, install and debug during experiments. XK-ME1 will help user learn kinds of technology, eg. motor drive, mechanical drive, pneumatic, touching screen control, PLC, sensor, frequency control etc. It offers one typical integration training environment for user to finish related technology training. XK-ME1 training system includes auto detection technology, pneumatic technology, PLC, electrical control circuit, inverter application, touching screen application, auto control technology teaching, mechanical system installation and debugging and system maintenance & faults detection training items. TECHNICAL PARAMETER Working Source: Three phase five wire system AC 380 V±10%, 50 Hz; Training table overall size: 1200mm×800mm×840mm; Frame material: Aluminium steel; Whole set consumption apparent power: ≤1.5 KVA Safety protection measurement: Grounding protection, leakage overload over current protection; adopting high insulating safety type socket and high strength safety experiment wires. MAIN CONFIGURATION - Experiment table: aluminum steel structure, with roller, as the installation carrier of photoelectric integrated experiment device, each equipment can be free and flexible installation - The device is configured with a touch screen module, a programmable controller (PLC), inverter device, pneumatic device, sensor, pneumatic manipulator device, feeder, feeding transmission and sorting device etc. training mechanism. - Control part adopts touch screen module and a programmable controller (PLC), actuator is gas drive device composed of pneumatic electromagnetic valve - cylinder, it realize the whole system running automatically, and complete the sorting of the material - Material feeding unit: mainly includes the turntable, adjusting stand, DC motor, material and material discharging port sensor and materials detection support, etc. - Manipulator carrying unit: mainly including rotating cylinder, non-standard screws, pneumatic claw, claw magnetic switch, lifting cylinder, magnetic switch, throttle valve, telescopic cylinder, left and right limit sensor, cushion valve and mounting bracket, etc - Material delivery and sorting unit: mainly includes the magnetic switch, transmission sorting mechanism, discharging port sensors, discharging port, trough, inductive sensors, optical fiber sensor, filter pressure regulating valve, throttle valve, three-phase asynchronous reduction motor, fiber amplifier and pushing cylinder, etc - PLC and converter: brand user can choose as following: SIEMENS, Mitsubishi, AB, Schneider etc. - Touching screen: TPC7062KS, 7 inch color TRAINING ITEMS - Installation and debugging of pneumatic system project: Installation of the pneumatic directional control circuit; Installation of the pneumatic speed control circuit; Swing control circuit installation; Installation of the pneumatic sequence control circuit; Installation of the pneumatic manipulator device; Pneumatic system installation and debugging; - The installation of electrical control circuit and PLC programming projects: Motor forward and reversal control circuit connection and the control program written; Connection of motor speed control circuit and control program writing; Pneumatic direction control program writing; Pneumatic sequential control program writing; Pneumatic manipulator control programming; Belt conveyor control programming writing; Electromechanical integration equipment control program writing; Automatic production line control programming writing. - Mechanical and electrical equipment installation and debugging project Coaxiality adjustment of transmission device; Belt conveyor installation and adjustment; Carrying manipulator equipment installation and debugging; Sorting equipment installation and debugging; Feeding equipment installation and debugging; Automatic production line equipment installation and debugging - Automatic control system installation and debugging project Variety of sensors installation and debugging; Automatic control of the manipulator, Automatic control of belt conveyor Automatic control mechanical and electrical integration equipment; Installation and debugging of PLC control system; Installation and debugging of automatic production line
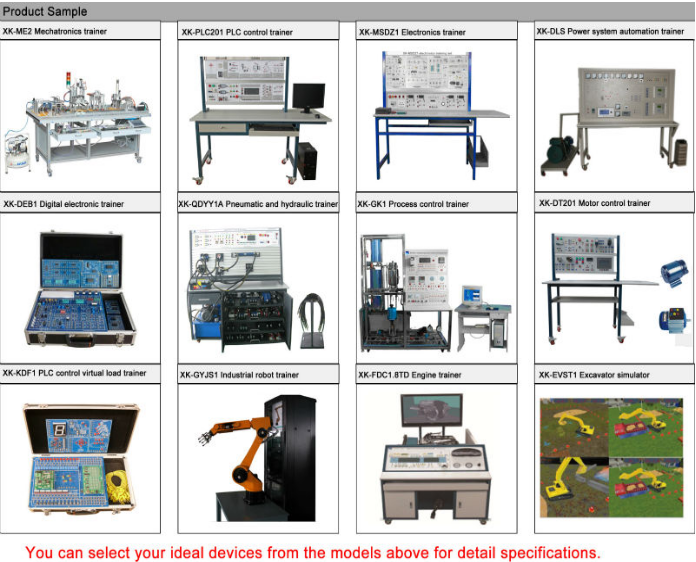
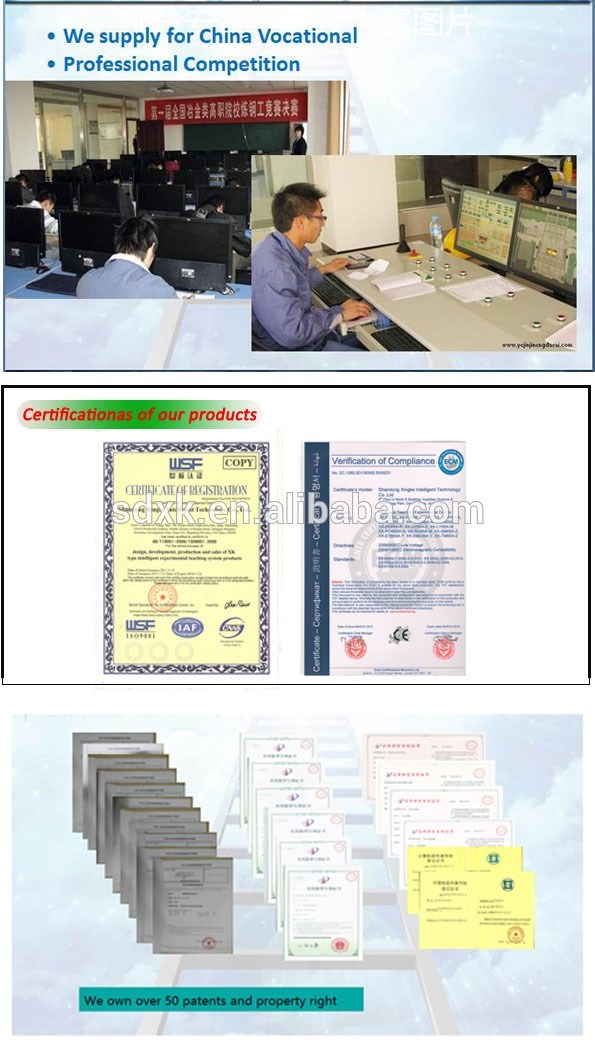