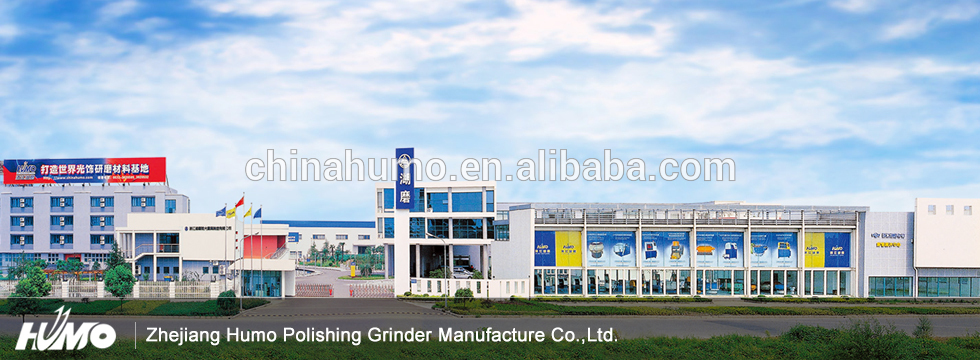
Product Description
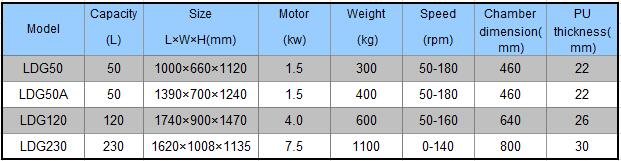
Introduction Humo centrifugal disc finishing machines provide 10 times effective faster grinding speed compared with conventional vibratory finishing machine. Centrifugal disc finishing machines are typically in small to medium size component surface finishing application. For special finishing requirement, the centrifugal disc finishing machine especially used for super fine and mirror finishing of specific component or component of special surface requirement 1. Processing unit (work bowl) The processing bowl is casted with DuPont hot moulded PU lining with thickness 20-25mm for long service time and high durability 2. Disc rotating system High speed control with optional speed inverter from Bosch Rexroth Adjustable gap between disc and ring 3. Water process system Compound/water dosing system available with tap PLC touch screen control with Siemens optional 4. Rigid machine construction Working principal The rotating disc with speed 60-250 RPM pushes the media and components mixture upward to the wall of processing bowl and downward to the processing bowl centre. With reduced acceleration force and enhanced gravity force mixture slides back down to the disc where it is again accelerated. Depending on disc rotation speed, the water level as well as media/compound combination, the finishing applications vary from fast grinding to super fine mirror polishing. The high energy centrifugal disc finishing machine offer productivity 10-30 times higher compared with conventional vibratory finishing process. Application The area of application including deburring, surface grinding, radiusing, and polishing of components with thickness around 0.2mm and larger gear components with more than 150mm. Typically stampings parts, casting parts as well as machined parts and tuned parts processed with high speed of the centrifugal disc finishing machine can achieve desirable performance in relative short processing times. Besides, it can achieve a high degree of automation with combination of different of other finishing technology according to user requirement. Feature Tilting angle of processing bowl up to 135° Optional circular pipe to rinsing and compound dosing Gap adjustment for machine for disc and ring Manual control unloading Possible install of separator screen with customized screen size and shape available Optional double layer screen available for remove undersize media Economical model for low budget application Product Pictures
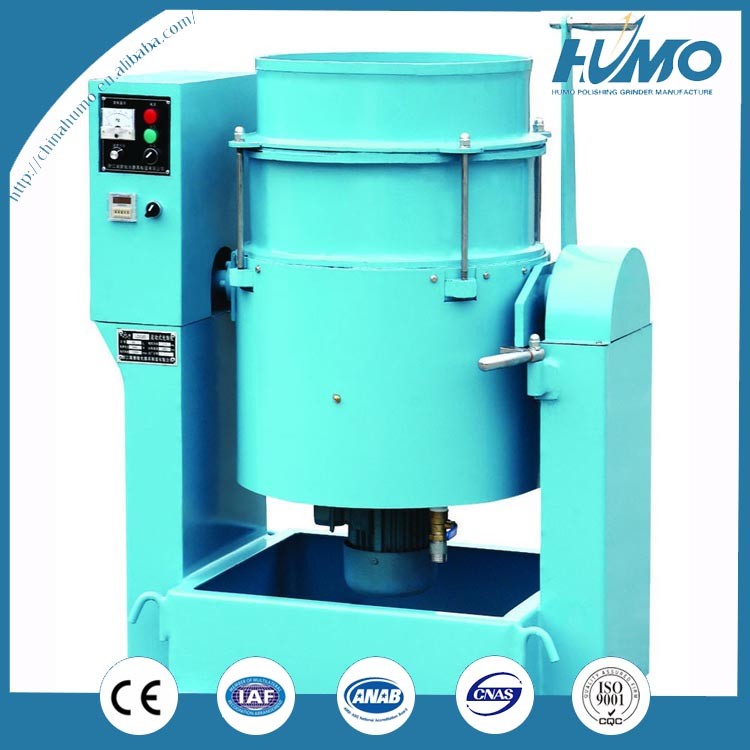
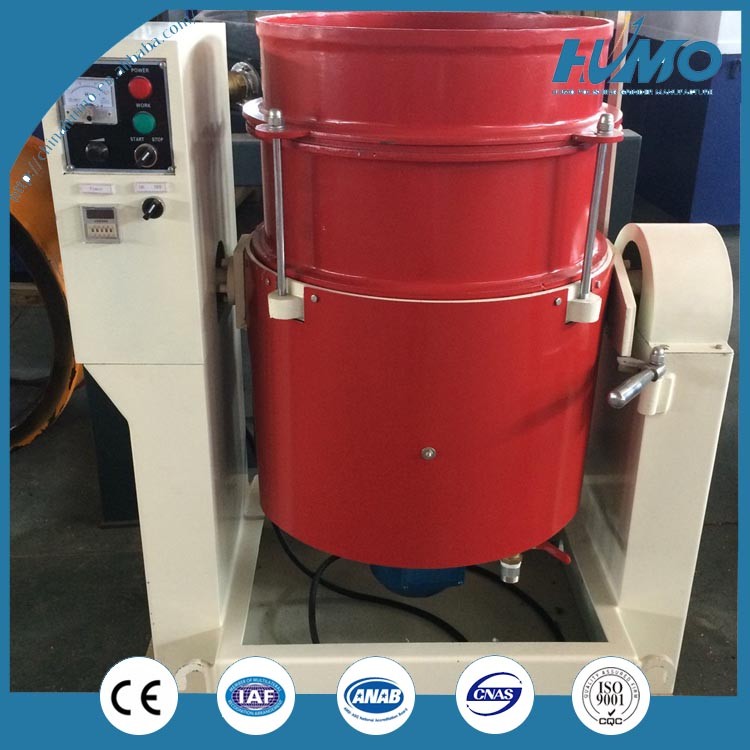

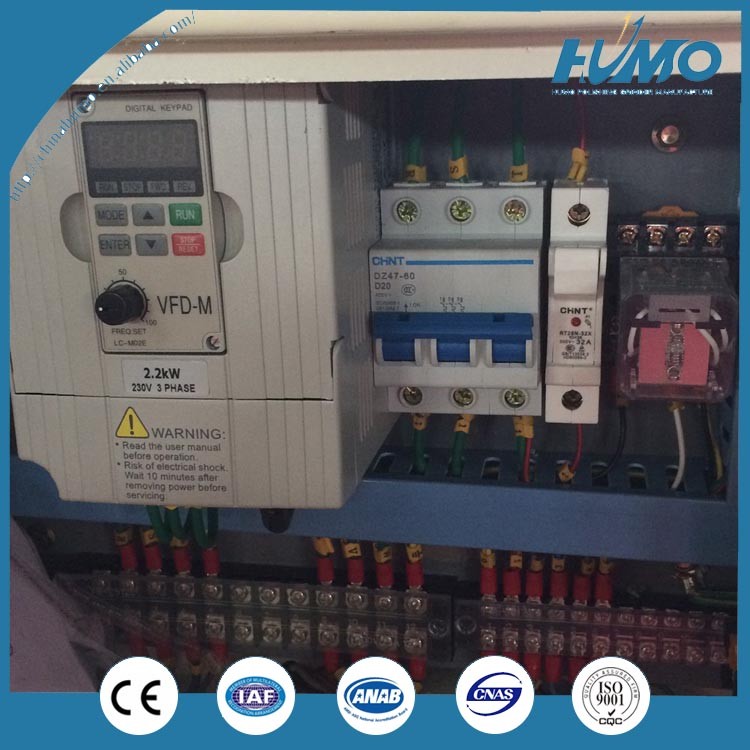
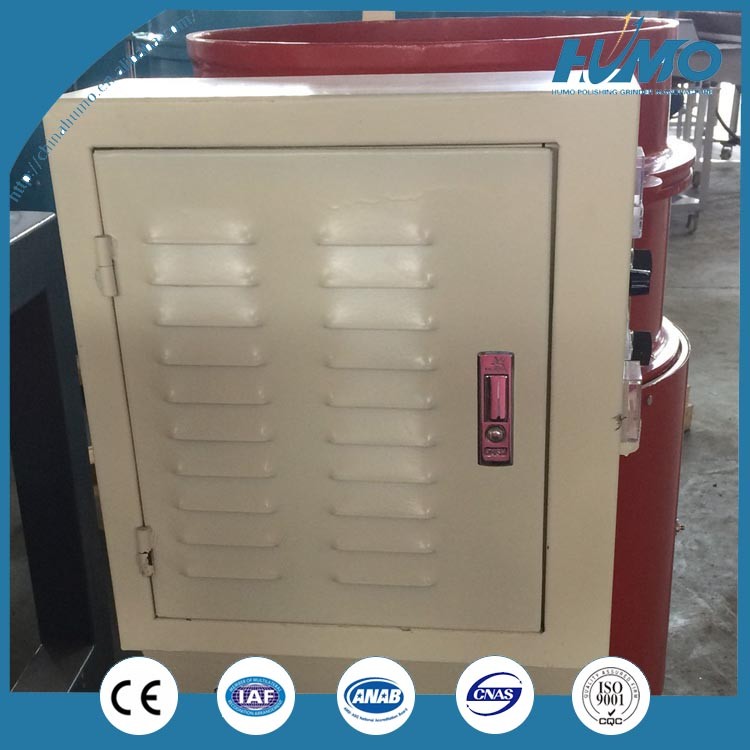
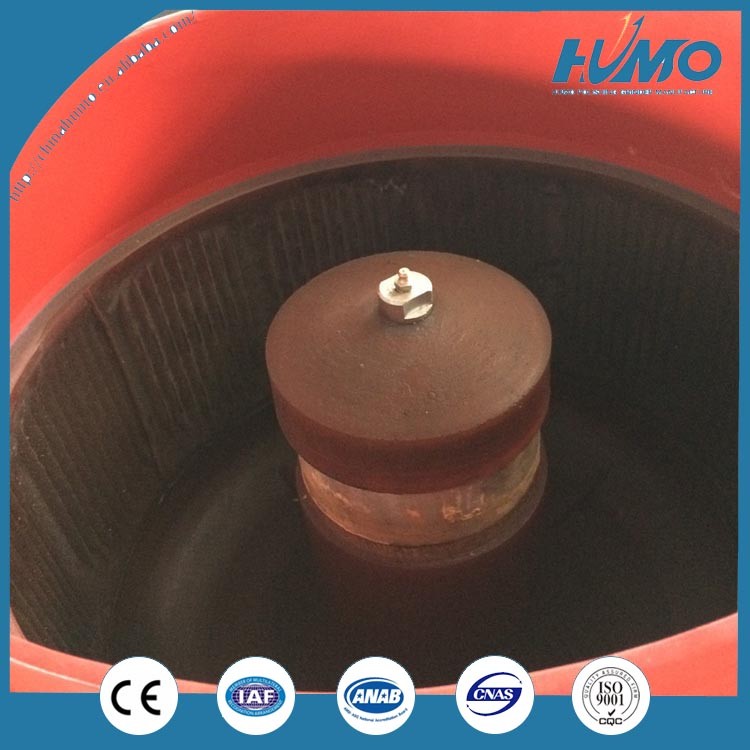
Production Process

Customer Processing Scheme
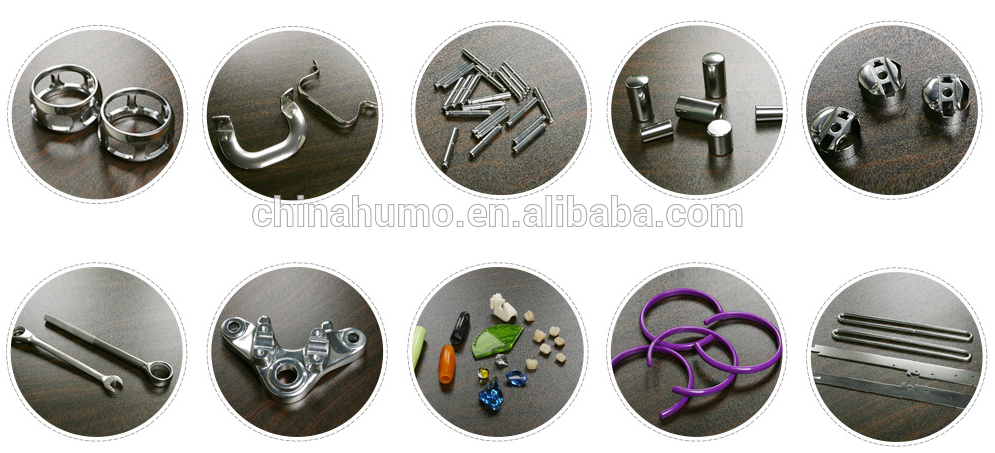
Company Information Zhejiang Humo Polishing Grinder Manufacture Co., Ltd. established in 1970s is one of the formulators of surface finishing industry China’s National Standards. Currently Humo Company has three production sites which cover an area of 156000 M2 and outputs over 30000 ton of grinding media, over 3000 sets of finishing machines, over 3000 ton of polishing compound and over 3000 ton of ceramic bead annually. The production scale among surface finishing industry is one of the largest in the world. Products sell well at home and abroad, such as America, Japan, Korea, Australia, German, Switzerland ect, over 50 countries totally.
Humo Company dedicates to providing high quality products and advanced technology on surface polishing for customers and manufacturers from all types of industries. Over thirty years’ professional experience in the area. Humo systematically research new applications for technologies and develop innovative process solutions, which combine consistent surface quality with the highest level of economic feasibility. Humo is proud of its surface process solution for comprehensive range of mechanical components, tailor-made solutions from small watch machinery accessories to huge earoengines casting part.
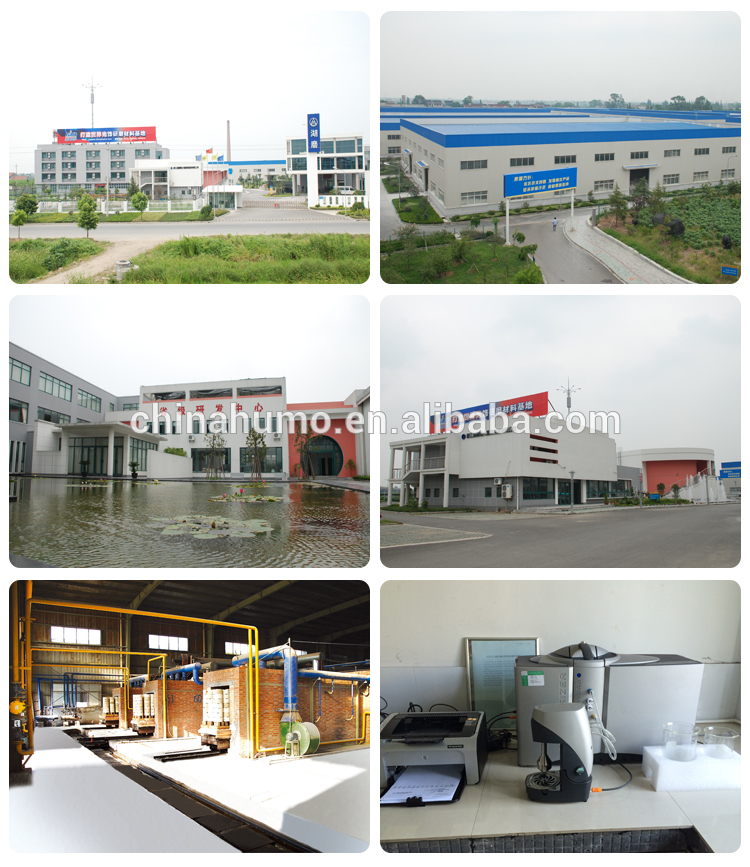
Our Customers
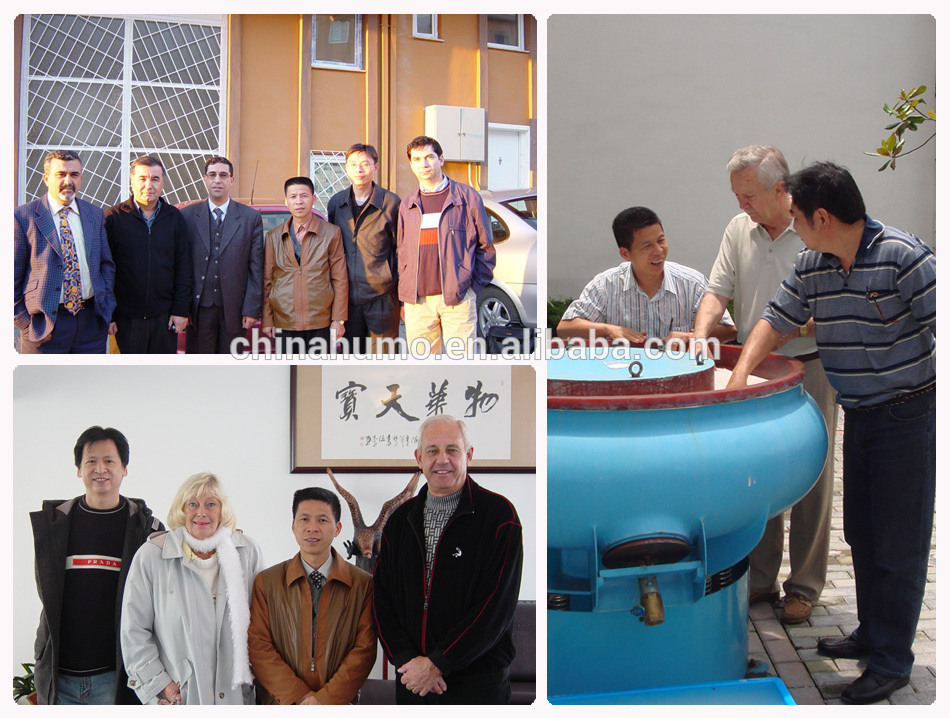
Certificate
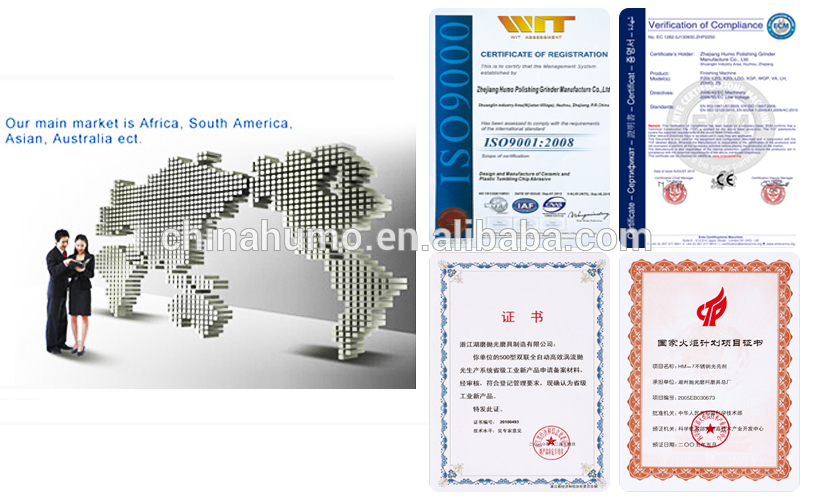
Packing information Wooden box packing and per customer requirement FAQ Our laboratory services are available to you at no cost. Mass Finishing and determination of Process Capability allows you to use the right media to ensure consistent production capability and built-in reproducibility of your manufacturing processes. We will work with you to determine the best media and the best processes for your parts. This step can result in: Reduced Cycle Times Improved RMS Finishes Reduced Finishing Costs Access to Latest Technology R & D for Special Process Media Mass Finishing describes a mechanical process where large amounts of parts are economically processed to achieve one or several surface improvement functions. These surface improvement functions include: Cleaning Deburring Surface refinement Inhibiting Drying
These functions are not independent of each other. It is common to have several or all of these functions take place in a single mass finishing process.
Process Capability is the measured, built-in reproducibility of the product turned out by the process. Such a determination is made using statistical data, not wishful thinking. Statistically determined limits are compared to specification limits to decide if a process can consistently produce acceptable product. Process capability is best established through closely monitored testing and recording of data over a set period of actually production.