Specifications rotary kiln process
Supplying scope:1.shell of rotary kiln
2.tire on the shell
3. Gearwheal.
4. Pinion
Rotary Kiln

Rotary Kiln Rotary kiln is refers to rotating calcining kiln (also known as rotating kiln), which belongs to thermal equipment. Rotary kiln can be divided into metallurgy kiln, chemical engineering kiln, and building material kiln according to its different dealing materials. The building material kiln is mainly used in calcining clinker cement, limestone and porcelain granule. Metallurgy rotary kiln is mainly used for the magnetizing calcining of lean iron ore in iron and steel plant in metallurgy industry, the chromites and josephinite oxidizing calcining , calcining of dewalquite and clinker aggregate and aluminum hydroxide roasting in aluminum factory; Chemical engineering rotary kiln is used in chemical plant for chromium ore and chromium ore powder roasting. The limestone kiln( activity limestone kiln ) is used for calcining activity lime and dolomite in iron and steel plant and ferroalloy works Rotary kiln is the equipment which is widely used for dealing with solid material mechanically, physically and chemically in building material, metallurgy, chemical, engineering and environment protection industries. Metallurgy Rotary Kiln Detailed Product Description Metallurgy rotary kiln also known as roller rotary kiln Metallurgy rotary kiln: It is mainly used in lean iron and oxidized ore magnetizing calcining; the chromites and josephinite oxidizing calcining; calcining of high metallurgy ore in refractory works; calcining of dewalquite and clinker aggregate and aluminum hydroxide calcining in aluminum factory; chromium ore and chromium ore powder in chemical plant. Magnesium Rotary Kiln Detailed Product Description Our company owns the magnesium production line. The raw material{dolomite} which is the qualified material crushed by the crusher is calcined into white by rotary kiln, cooled by the cooling machine and then mixed evenly with silicon powder (75%) and silica powder (including GaF2 fluorite=95%). Being grinded into powder by ball mill, the marble machine will shape it as a ball which will be put into the reducing furnace after being equipped with the heat-resistant and stainless steel reduction jar. Then crude magnesium is restored and formed under the temperature of 1200-1250 degree celsius and vacuum of -1.33PAa. By solvent refining, ingot casting and superficial treatment, the magnesium ingot is formed. Bauxite Rotary Kiln Detailed Product Description This series of rotary kiln mainly consist of rotary bowl, supporting part, gearing, rotary hood, rotary hood and end sealer, and combustion device. Kiln eye frame cover is made in the form of block and it is easy to install. It is of high heat-resistance, corrosion resistance, and wearing resistance. The cooling wind in the kiln hood packaged air conditioner can cool the kiln hood bowl and kiln eye frame cover evenly which prolong its use span. Kiln hood cover adopts bulk mode which makes the air moving more stable. The kiln hood and kiln end sealing introduces the double sealing method of radial friction labyrinth and flap. With simple structure and easy maintenance, the double sealing is the most advanced sealing method inland. Mineral Roasting Rotary Kiln Detailed Product Description: In order to lower the operation cost, the series of rotary kiln mix block with powder in calcining. The green ore measured by the electronic belt scale, belt conveyor, steady bunker, and air lock valves in the reservoir will be fed into rotary kiln end directly. The steady bunker is located only in kiln end in order to lower the cost. Ore put into the rotary kiln will be heated first. Ore in the kiln moves oppositely to the hot air. Ore is heated to the reduction temperature in the heating area and then enters into the reduction area where the temperature of the central flame zone is kept at about 1000 degree celsius and the temperature of the steam zone is kept at about 700 degree celsius . Then the ore is reacted with the reduction gas and become magnetic ore for dressing by magnetic separation. Nickel Rotary Kiln The technics of dealing with nickel by rotary kiln are as follows: Fetch the nickel and mix it with lime; filter the mixture and put the powder agglomates into the rotary kiln chamber directly, crush the block into powder agglomates and put them into rotary kiln chamber; crush the coke and put them into rotary kiln chamber; deliver the powder agglomates and coke; put the powder agglomates and coke together into the first-degree mixture bowl to be mixed; after the first-degree mixture then comes to the second-degree mixture and some water should be added to keep it moisture; deliver the mixed material into the rotary kiln and inlet the hot coal gas to reduction calcining; put the roasted product into the hot furnace to smelt.
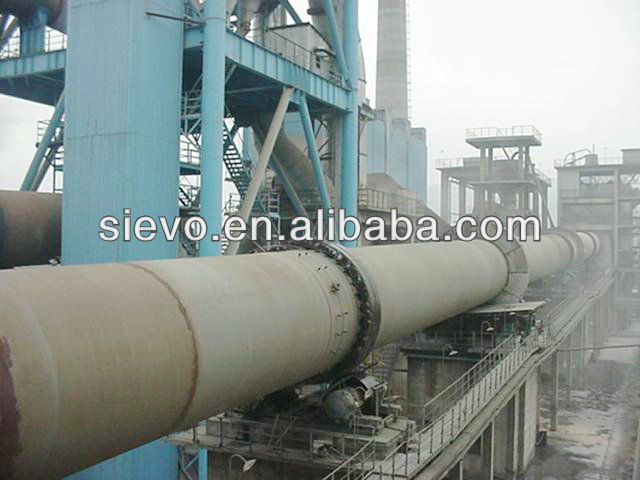
Building Materials Rotary Kiln The building material rotary kiln is mainly used in cement industry, such as lime kiln, cement kiln and mud kiln. In the building material industry, besides calcining clinker cement, it can be used to calcine clay, limestone, and dry slag. It also can be used to produce ceramsite which can take the place of the green carpolite and sand and add the building toughness and earthquake-resistance performance function In the production of refractory material, rotary is used to calcine the material, making it stable in dimension and solid in strength. Then it is reprocessed and made formation. Lime Rotary Kiln Lime Rotary Lime Rotary Kiln Technical Features: 1. With advanced structure, the low pressure loss of the vertical preheater can speed up the preheating process, the decomposition rate in the kiln of the preheated limestone can be 20-25%, and can use directly the 10-15mm fine grade limestone. 2.Both ends of rotary kiln is sealed by combination scale, which ensures the index of air leakage less than 10%. In order to lessen the radiation loss, it adopts compound refractory materials 3.Round or square vertical cooler with filling type and ventilated area, which make the lime temperature 800 degree celsius + ambient temperature. It is easy to transport, store, and can be preheated the secondary kiln air to above 700 degree celsius , which reduce the moving parts and special materials Cement Rotary Kiln Cement rotary kiln belongs to the building material equipment. Cement rotary is the main equipment in the dry production line of clinker cement. This series of rotary kiln consist of bowl, supporting part, supporting device with catch wheel, gearing rigging, flexible kiln hood, kiln hood and kiln end sealing device, nozzle device and so on. The rotary kiln is higher than the horizon as the whole body is supported by the riding wheel with the catch wheel controlling the up and down move of the kiln body. Besides the main transmission, the transmission system sets auxiliary transmission device which can keep the kiln body move when the main power is off to protect it from bending deflection. The kiln hood and kiln end sealing device adopts advanced technology which ensures the security of the sealing. Cement rotary kiln is of solid structure, stable operation, and high quality output product. Mud Rotary Kiln Technical Features: Mud is the waste of paper-making factory. Due to the high contents in silicon dioxide and other impurity, the lime recycling is hard. Presently, most factories just transport and bury the mud. The problem is the factory need investment to the mud bury and the secondary pollution after burying affect the local people life and this may lead to environmental-protection department investigate. How to deal with the mud bothers the factories for a long time. After many years study, our company introduces the key technology of mud rotary kiln from aboard and has produced the series of alkali recycle mud calcining rotary kiln with proprietary intellectual property rights. This technology offers new way for the multipurpose use of burweed alkali mud recycle, which has obvious social benefit and good economic benefit. Chemical Rotary Kiln Chemical rotary kiln is used for calcining minerals in chemical engineering factory, such as: zinc oxide, titanium dioxide, kaolin, aluminum acid calcium etc. The rotary kiln of our company features in simple structure, easy control production process, less wearing parts, high service factor, and high quality. We have professional engineer to design product for you and will send professional man to install for you. With first-class quality and perfect after service, we are waiting for you consultation.
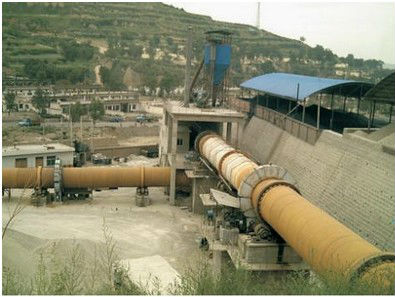
Zinc-oxide Rotary Kiln The technics of producing zinc oxide by rotary kiln are as follows: Crush the zinc charging and the coke coal into powder lot less than 40. Mix the zinc charging with the coke coal pro rata 1:0.30~1.35 evenly and make the mixture into granule with diameter being 8-15 mm. In the end, put the granule into the brick kiln to smelt and produce zinc oxide. This technics greatly saves the coke or fire coal. The product gained by smelting is of fine quality and high productivity. Titanium Dioxide Rotary Kiln Detailed Product Description The structure of titanium dioxide calcining kiln is similar to the rotary kiln in alumina and cement industry. The bowl is made up of armor plate coil with fire-resisting lining inside and slant to the horizon. The bowl is set with belting leather and the bearing is on the bearing device of its corresponding gear. Fix a bull gear with a tangential spring board on the bowl around the central belting leather which is jointed with the pinion bellowing. In normal operation, the main transmission electric motor transmits motion onto the open type gear by the main speed reducer thus drive the rotary kiln. The working principal of titanium dioxide rotary kiln: Send the filter pressed titanium dioxide filter mass to the rotary kiln end (the high end of the bowl) meanwhile the combustion nozzle in the kiln hood (the lower end of the bowl) blows the clean fire and hot wind to the kiln and dehydrates and calcines the filter mass. The titanium dioxide filter mass after being dehydrated and calcined under the high temperature of above 1000 degree celsius can turn around the circle and move with the axial direction( from the high end to the low end) by the slanted rotary kiln body. Being continuously like that , the dehydration and calcining will be finished. Finally through the double hydraulic pressure reverse turning bed discharge valve in the lower part of the kiln hood cover, the material enters into the cooling machine. The titanium dioxide is made after being cooled and filtered. Kaolin Rotary Kiln The features of the high purity kaolin: high white content, soft texture, easy to disperse and suspend in the water, fine plasticity, high cohesive property, good electric insulation property; excellent anti-acid solubility, lower base exchange capacity, and pretty good refractory nature and such physicochemical property. So kaolin has become a must ore raw material in paper-making industry, ceramic industry, rubber industry, chemical engineering industry, paint industry, medical industry, defense industry and so on. Kaolin rotary kiln(bauxite rotary kiln/ magnesia rotary kiln/zinc oxide rotary kiln) with internally heated rotary kiln calcining superfine kaolin by medium temperature(950 degree celsius-1050 degree celsius), and technics being maturity and advancement inland, is a leader in the superfine kaolin calcining technology which is energy-saving and of high production. Calcium Aluminate Rotary Kiln Detailed Product Description The chemical composition of calcium aluminate is AL203 and CaO which have strong activity. The acid-solution method of producing water purification agent can greatly save the human race and electric power, as well as cut the cost. With easy equipment and manipulation, it is the ideal raw material to produce polyaluminium chloride. The products of calcium aluminate can be categorized into water treatment, steel-making and deslagging and high alumina cement. The production method: crush the proportioned alumyte and limestone, make them into ball and send them into the rotary kiln. Cool them after calcining at the temperature of 1300 degree celsius. The calcium aluminate is produced after crush and package. This series of equipment consist of bowl, supporting device, supporting device with catch wheel, gearing rigging, flexible kiln hood, kiln hood and kiln end sealing device and combustion device. It have features of simple structure, stable operation, and easy control in product process.

Energy-saving Rotary Kiln The potential advantages of the energy-saving rotary kiln With the greatly increase of the price of energy, it brings great pressure to the lime production enterprises, who face great challenges of their survival and development. With the more powerful inspection about the environment, the operation of enterprises becomes more difficult. Thus, it is very important for the enterprises to seek a new kind energy-saving, and environmental-protection active lime calcinations process. So it breaks the traditional lime production process by absorbing the energy-saving and environmental-protection lime production plant with vertical pre-heater and vertical cooler. And it has already been recognized by the enterprises. Efficiency of Energy-saving Rotary Kiln. The applicant of energy-saving rotary active lime kiln decreases the coal consumption and exhaust emission .It cleans up the tail gas with pulse jet bag filter and has passed the actual operating measurement. The productivity rises about 30%,the energy is saved about 40%, and the area is saved about 40% which achieves the aims of energy-saving, high-efficiency, environmental protection. This kind of calcinations is the more advanced process in nowadays'active lime production and worthy to be popularized. Ceramic Sand Rotary Kiln Detailed Product Description At present the production equipment of ceramic sand is industrial rotary kiln. The columnar main kiln body has 2 degree obliquity angle to the level standard and is placed on the carrier roller. The material is sent into the kiln from the high end. As the kiln is doing swivel motion, the material rolls from the high place (kiln end) down to the lower place (kiln hood). Meanwhile in the kiln hood, the nozzle sprays the gas into the kiln to make it blaze fully. The heat produced makes the material change physically and chemically, and the ceramic sand is formed after the material being cooled down. Drying Rotary Kiln This series of rotary kiln is an important equipment widely used in the manufacturing process of metallurgy, chemical engineering, cement, and food. For its difficulty in self-control, it is mostly controlled artificially or some control loop is controlled by analogue instrument. The change in thermal current's speed and temperature of drying medium is the main factor affecting the operation and drying quality of drying rotary kiln in the manufacturing process of drying rotary kiln. The guiding theory of drying rotary kiln's temperature field control: by controlling the distribution of thermal current's speed and temperature of drying medium in rotary kiln and the quality of the gas combustion, a stable and appropriate drying environment can be formed in the kiln, that is temperature field, to satisfy the demand of drying technics. Dry-process Rotary Kiln Compared with the wet-process rotary kiln, the dry-process makes the raw meal into the raw drymeal which has less than 1% moisture content. So it saves the heat needed in evaporation of water in the wet-process. The hollow type kiln has a lager amount of heat consumption due to its high temperature of waste gas. The dry-process makes the raw material into drymeal whose fluidness is worse than slurry and can not be mixed well.
Model | s | Electrical motor | otal weight (excluding refractory brick)t |
Main driving (r/min) | Slope of the kiln shell% | Capacity(t/h) | Model | powerkw | Speed regulation ranger/min |
Φ1.9/1.6x36 | 0.53-1.59 | 4 | 2.5-3 | JZT-72-4 | 30 | 1200/400 | 53 |
Φ2.1/1.8x36 | 0.5-1.51 | 4 | 4 | JZS-81 | 30/10 | 1410/470 | 75 |
Φ1.2x25 | 0.5-1.6 | 3 | | JZTY71-4 | 22 | 1200/120 | 34 |
Φ1.6x32 | 0.158-0.258 | 3 | | JZJY61-4 | 15 | 1200/120 | 46.82 |
Φ1.8x45 | 0.66-1.98 | 4 | 3.5 | JZS-81 | 30/10 | 1410/470 | 80 |
Φ2.2x50 | 0.125-1.25 | 3.5 | 4 | YCT280-4A | 30 | 1320/132 | 130.71 |
Φ2.5x50 | 0.516-1.549 | 3.5 | 5.5 | YCT355-4A | 55 | 1320/440 | 167.5 |
Φ3x48 | 0.3309-3.309 | 3.5 | 35 | ZSN4-250-21B | 90 | 1000/100 | 237 |
Φ3.3x52 | 0.391-3.91 | 3.5 | 50 | ZSN4-315-082 | 190 | 1000/100 | 280.8 |
Φ4x60 | 0.396-3.96 | 3.5 | 104 | ZSN4-355-092 | 315 | 1000/100 | 487.5 |
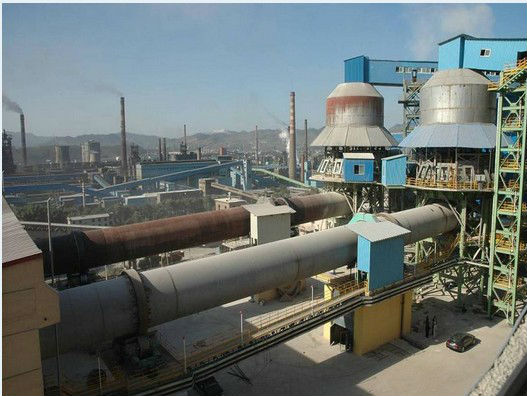
rotary kiln process