Specifications Hematite iron ore beneficiaiton:
1. Magnetic Roasting process;
2. Final Fe grade 62% up;
3. Low water comsumption
Hematite Iron ore Beneficiation Equipment 1. Technical Working principle – Hematite/limonite ore is the mineral form of iron oxide (Fe2O3) which is one kind of weakly magnetic strength, it is hard to be separated with normal magnetite separation process. For this kind of ore, we suggest magnetic roasting process plus grinding process and magnetic separation process to get the final high grade of Fe concentrate. – Magnetic roasting is heating the ore up to certain temperature to create physical and chemical reaction under the reducing agent. With this process, the magnetic property of iron minerals will be significantly enhanced, however, for the magnetic property of gangue minerals, there is no change. Therefore, various weakly magnetic minerals can be efficiently separated after magnetic roasting process. For this magnetic roasting process, rotary kiln is the key equipment for it. – For Hematite/limonite ore, with the help of coal as reducing agent, it can begin deoxidizing in reducing atmosphere at the temperature of 400degree, and when the temperature reach to 570degree, it can easily be changed into magnetite ore. At temperature of 800-900degree, Hematite/limonite ore can be changed into magnetite ore.
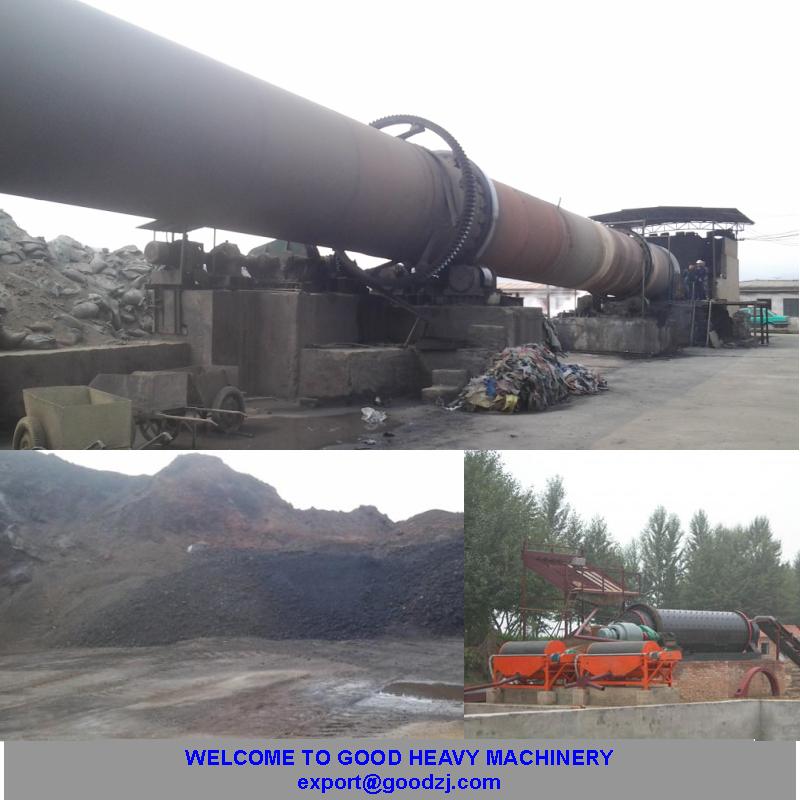
2. Rotary Kiln Operation The rotating speed of kiln has great effect on materials residence time, reaction speed and reaction extent. For fast rotating speed, the residence time of materials in kiln is shorter, although the materials has good upside-down, but, it can not be in full reaction. For low rotating speed, the residence time of materials in kiln is longer, and it can be in full reaction, however, the kiln has lower productivity. For example, for kiln size of 2.8x45m, the residence time of materials in kiln is about 50-90 min. and the rotating speed is suitable at 1-1.5r/m. From the kiln inlet part, it is divided into fours zones, includes drying zone, preheating zone, reaction zone, cooling zone. Of which, reaction zone is longest and with highest temperature. Normally, the reaction temperature is 800-900 degree. The gas at kiln inlet is about 300-450 degree. See below Figure (just for reference).
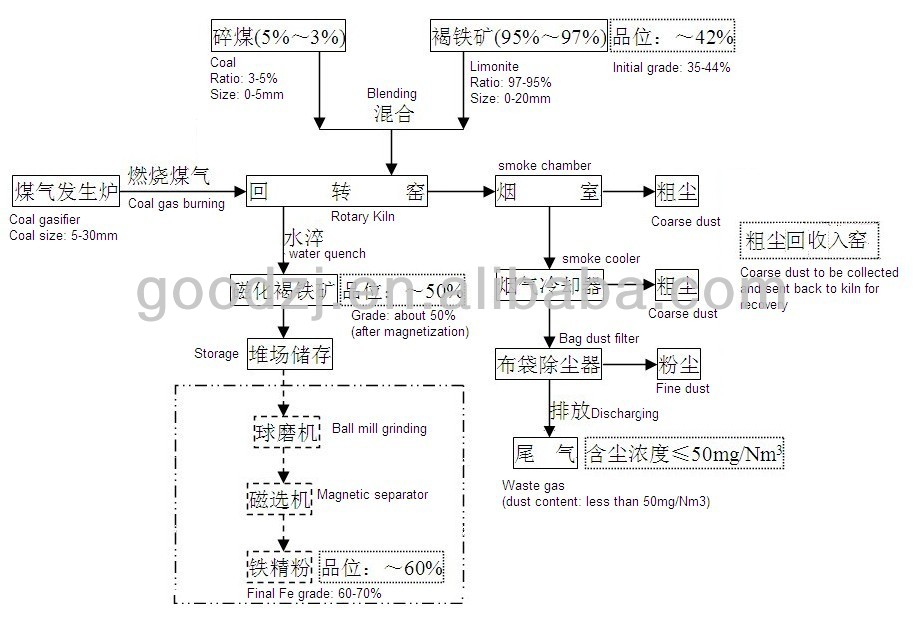
3. Chemical Reaction in Rotary Kiln In rotary kiln, under the high temperature of 800~900°C, and with help of reducing agent of coal, Fe2O3 is reduced into Fe3O4. In this process, attached water and crystal water in the ore is firstly removed. The main Physicochemical process are as follows: Fe2O3·nH2O(H2O)+ heat → Fe2O3·nH2O + H2O↑ (removing attached water) Fe2O3·nH2O + heat → Fe2O3 + nH2O↑ (removing crystal water) C + 6Fe2O3 → 4Fe3O4 + CO2↑ + heat (reduction magnetization)