AAC Blocks Manufacturing Machine Plant
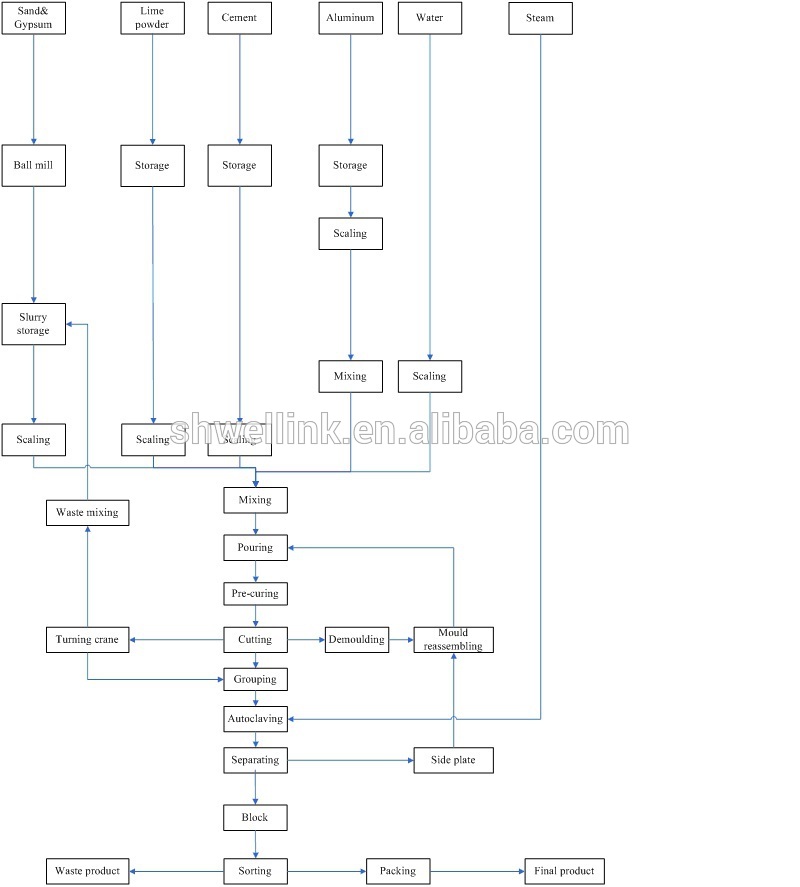
Automatic AAC Block Plant Making Machine :flowchart Product Description Raw Materials The main materials are sand, cement, lime and aluminum powder. 1. Cement 425 # cement shall be acceptable. 2. Sand The sand shall be requested as standard JC/T 622<sand for silicate building products>, The more quartz content, the better result of production. Table3-1 Chemical content of sand
Chemical Class | SiO2 % | K2O+Na2O % | Organic compound | Mica % | SO3 % | Mud % | H2O% |
excellent | ≥85 | ≤1 | Suitable | ≤0.5 | 1 | 3 | 8 |
I | ≥75 | ≤3 | 5 |
II | ≥65 | ≤5 | ≤1 | 2 | 8 |
Table3-2 Granulation of sand
Granulation Class | Percent % |
Excellent | I-Class | II-Class |
2.5~5.0(Round hole) | 0 | 0 |
1.25~2.5(Square hole) | 10 | 10 |
0.16~0.25(Square hole) | 60 | 45 |
<0.16(Square hole) | 30 | 45 |
3. Lime The lime shall be requested as JC/T 621-2009<lime for silicate building products>. 4. Aluminum powder The aluminum powder shall be requested as JC/T 407-2008<aluminum powder for AAC>. General Processing Description 1. After crushing, the lime & gypsum grains are stored in vertical silo, the granularity should be no more than 25mm. Then the grains are fed into ball mill by separate belt scale, and will be sent to granular cementation silo when granularity reaches 3500~4000cm2/g. 2. Mill the sand to slurry in wet ball mill and put the slurry into tank for storage. 3. Add the sand slurry, granular cementation materials & cement which are scaled as per proportion into the casting tank equipped with stirrer for mixing, a certain amount of steam should be entered into the stirrer for increasing the raw materials temperature to 40~45℃. 4. After mixing of 3~4min, open the discharger valve of aluminum powder, feeding into the tank, and continue mixing about 40 seconds, then pour the mixed slurry into mould for casting. The whole cycle is 6~8min. 5. Transport the casting cake with mould to curing zone for foaming and concreting, environment temperature is 40~45℃ and curing time is 90~150min; and then pull out them from the curing zone when the strength reach the lowest cutting strength. 6. Transport the mould with casting cake to cutting zone. A titling machine separates the cake from the mould and put the cake onto loading car after 90 degree overturning. After vertical cutting & cross cutting the cake turns into blocks (L ± 3mm ~ W ± 1.5mm ~ H ± 0.6mm), then the ground turning device turns 90 degree and place the blocks onto autoclave base plate. 7. The loading car transports the cakes into autoclave with temperature 190℃ and steam pressure 1.2MPa, autoclaving cycle is 12H. The tail steam of the autoclave will be recycled into other autoclaves and/or to curing zone by pipe for completely utilization. 8. After autoclaving, the blocks are put in different stacks, and the separate moulds are transported to mold cleaning zone for cleaning and continuously production. 9. The waste materials will be collected into a waste slurry tank, where mixed with fresh materials in a correct proportion for further production. 4.2 Technological data Mixing cycle: 6 ~ 7 minutes Casting temperature: 40 ~ 45℃ Curing time: 2.5 ~ 3.0h Environment temperature for curing: 45 ~ 55℃ Autoclave loading /unloading: 0.5h Vacuuming: 0.5h (0 ~ -0.05MPa) Pressure up: 1.5h (0.06 ~ 1.2 MPa) Constant pressure: 7h (1.2 MPa) Pressure down: 1.5 h (1.2 ~ 0MPa) Total: 11h
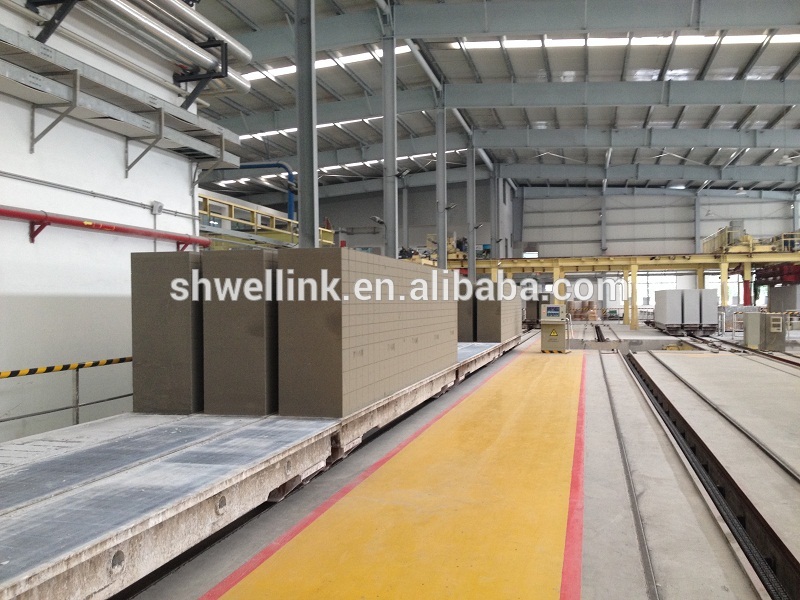
Lower Price High Quality AAC Block Production Line :workingsite AAC Block Cutting Machine/AAC Block Making Machine Pro AAC Block Panel Pouring Mixer/AAC Block Production Line Process Typical stages involved in the AAC panel production process include raw material preparation, batching and mixing, pouring, pre-curing, cutting, autoclaving, and packing.
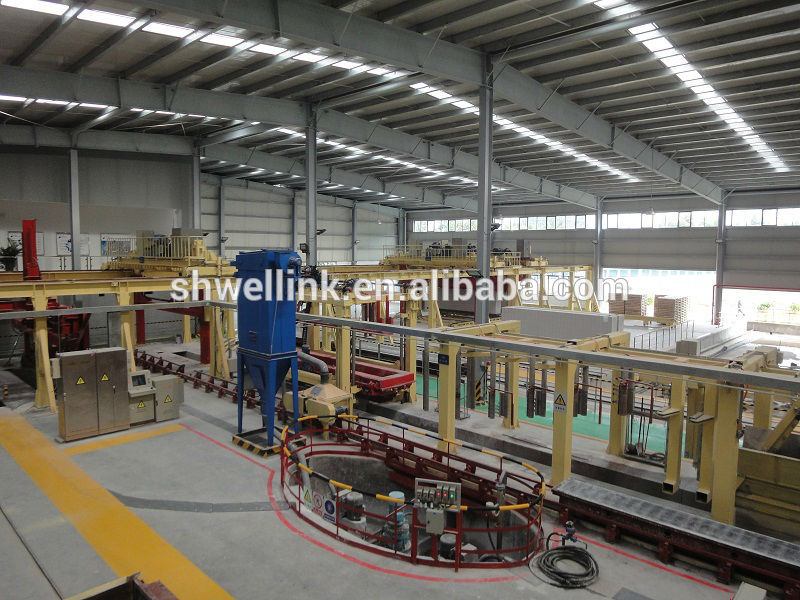
Lower Price High Quality AAC Block Production Line : overview Batching Pouring Mixer The pouring mixer is a key element on the AAC block production line. It keeps the concrete from hardening by constantly tumbling the mixture around. In the mixer, ingredients of desired proportion are blended and then poured into the mould for pre-curing.
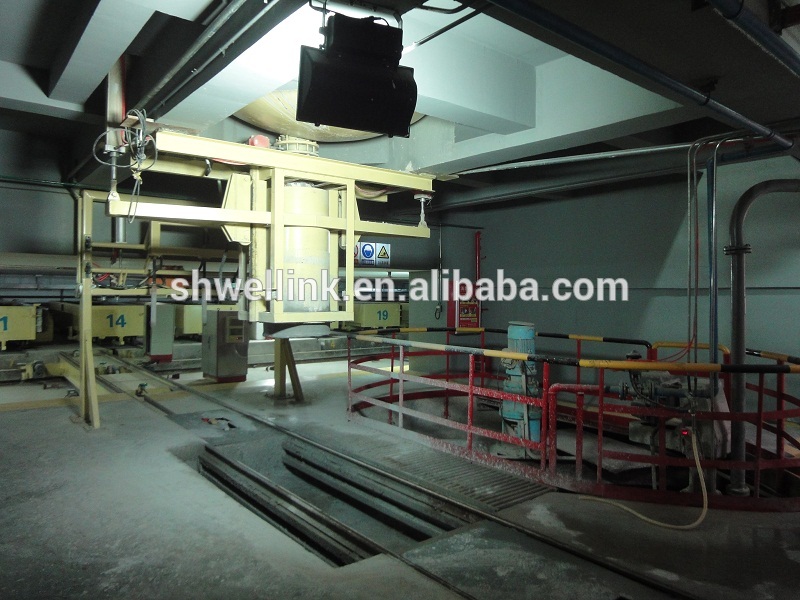
Lower Price High Quality AAC Block Production Line :pouring mixer Pre-curing and Cutting Mould The mould is a vessel into which concrete slurry is poured. In the mould, the slurry stiffens to form the green cake. The green care rises due to the evolution of hydrogen gas from the reaction between aluminum powder and rest of concrete slurry. The process is termed as pre-setting.
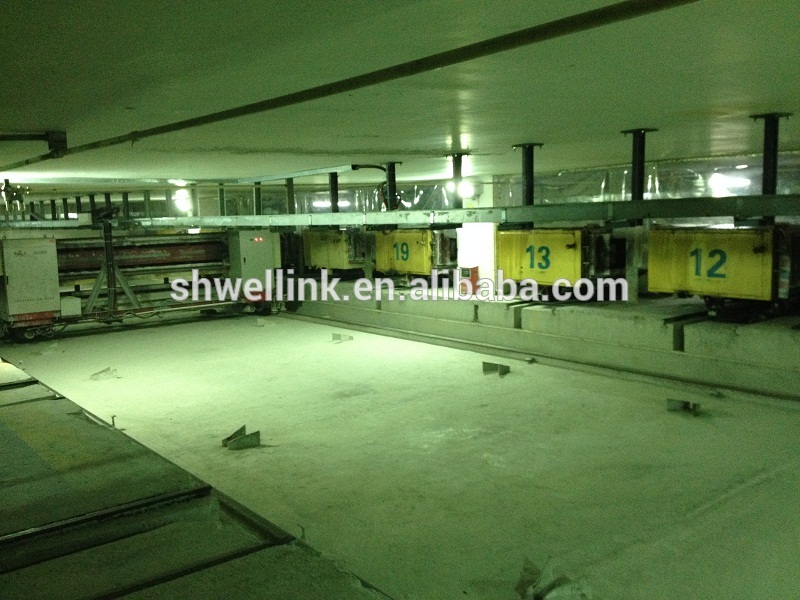
Lower Price High Quality AAC Block Production Line :mould Mould Turning Machine The mould turning machine is mainly used to turn the pre-set concrete through 90 degree so that the mould can be easily removed from the concrete to facilitate cutting. This process leaves two side plates of the mould on the concrete. The purpose of side plates is to support the preset concrete and keep it from collapsing. After de-mould, the incomplete mould combines with two new side plates to form a complete one again, which readily accepts the next concrete pouring.
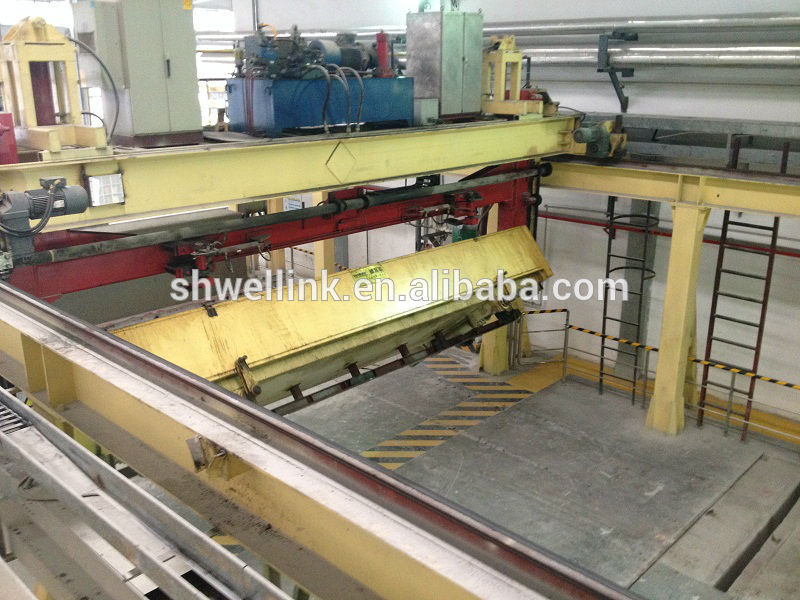
Lower Price High Quality AAC Block Production Line :mould turning machine Cutting Machine The cutting machine is used to precisely cut all the six sides of concrete cakes to various required dimensions. It is mainly made up of transfer car, vertical cutter, cross cutter, and car exchange device.
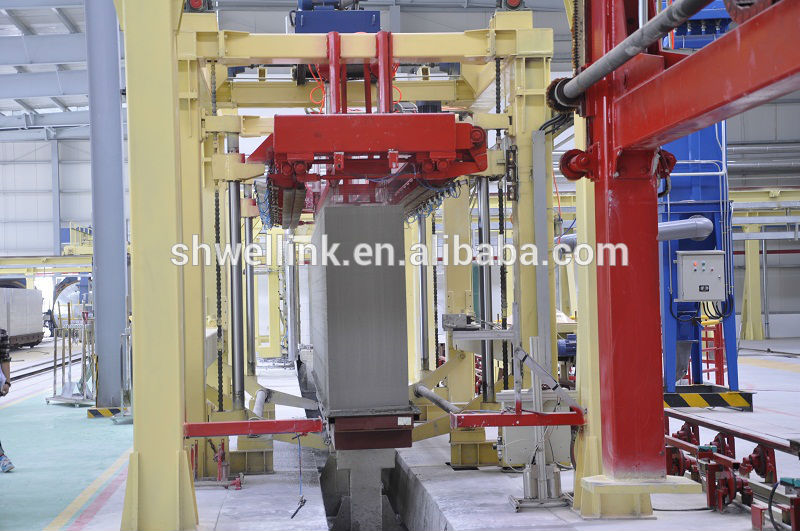
Lower Price High Quality AAC Block Production Line :vertical cutting machine Tilting Table for Semi-product As the cutting is completed, the green cake is tilted back by 90° so that it sits on its wide, lengthwise side. At this point, a scraper is used to remove the bottom waste as well as clean the bed. Wastes that are washed off into the pit will be recycled, which results in cost savings. All these motions are driven by hydraulic cylinder and controlled via proportioning valves to ensure stability. The big transfer car, small transfer car, tilting bed, and scraper are the major parts that make up the whole tilting system.
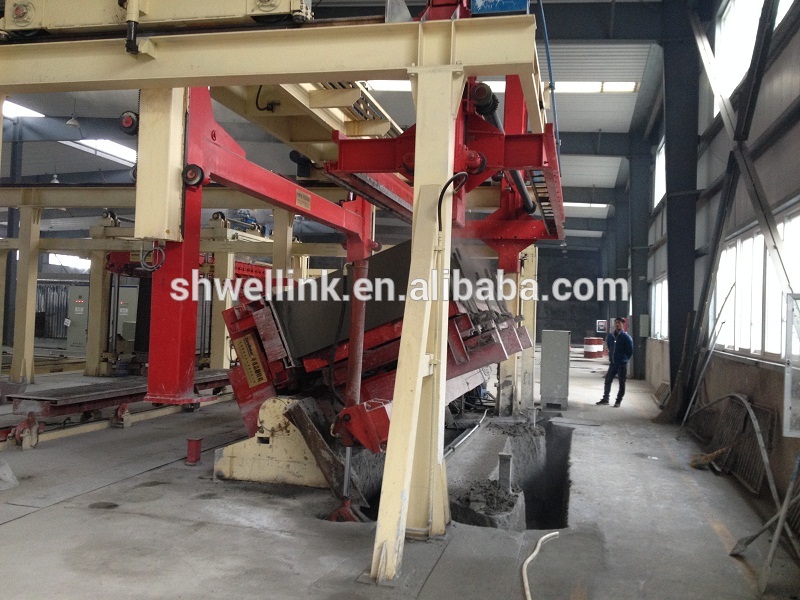
Lower Price High Quality AAC Block Production Line :tilting table for semi-product Stacker for Semi-product The stacking machine is used to transfer the concrete panel together with the bottom plate of the mould to the de-moulding crane and the autoclaving car. It also returns the side plates of mould to the roller conveyor.
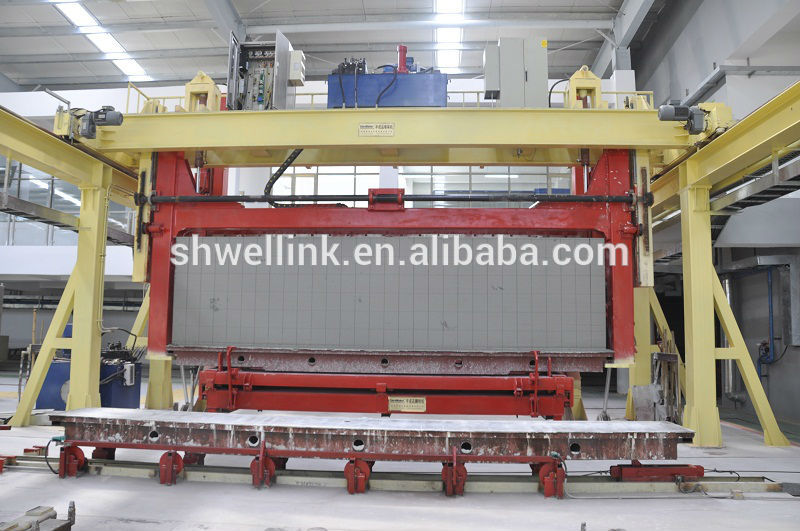
Lower Price High Quality AAC Block Production Line :stacker for semi-product Curing and Final Product Handling Curing Car The curing car, also known as autoclaving car, is an integral part of the autoclaved aerated concrete production line. It carries the semi-finished concrete panels (which are seated on the bottom plate of the mold) to the autoclave.
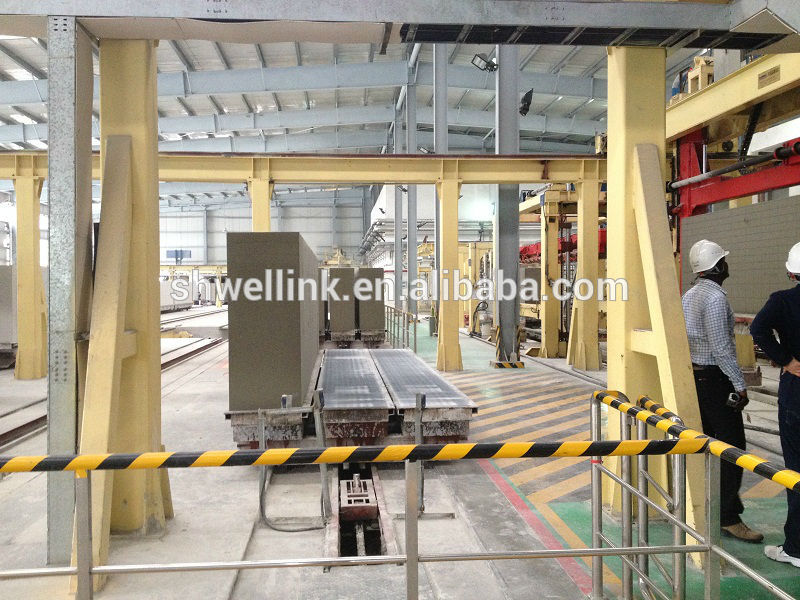
Lower Price High Quality AAC Block Production Line :curing car Ferry Car The ferry car is a kind of material handling equipment that travels across the line of AAC production. Thanks to this transfer trolley, the mould-carrying car and the cake-filled autoclaving car can run on each other’s rails.
Chain Conveyor In the chain drive system, the sprocket receives power from the motor and transmits it via the chain to the driven sprocket installed on the tow-car. The tow-car then pulls other equipment back and forth along the rail, with the help of pushing and towing unit. Main parts of the chain conveyor include the transmission unit, towing unit (tow-car), and rear wheels. Autoclave Autoclave is a large steam equipment which can be used in steaming sand aac block,flyash aac block and aac brick/panel.
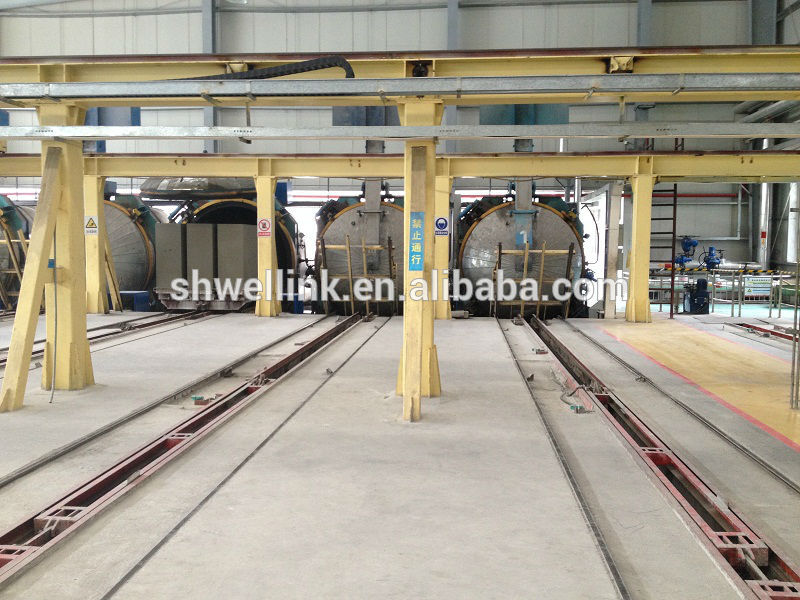
Lower Price High Quality AAC Block Production Line :Autoclave Separator After autoclaving, the piled-up concrete panels need to be separated along the cuts, one layer from the next. The purpose of separation is to keep each individual AAC panel from sticking to the adjacent ones. The separating operation is carried out by the separator, which is made up of the separating device and lifting device. The lifting motion of the separator is driven by a hydraulic power unit. Proportioning valves are used to control the hydraulic unit to ensure operating stability.
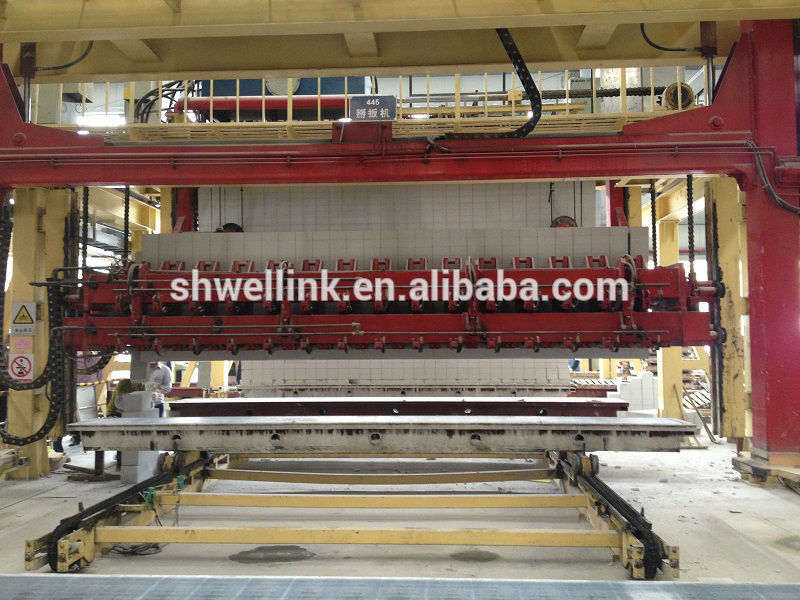
Lower Price High Quality AAC Block Production Line :separator Clamping Machine The clamping machine takes hold of each individual AAC block/panel and carries it to the packing line.
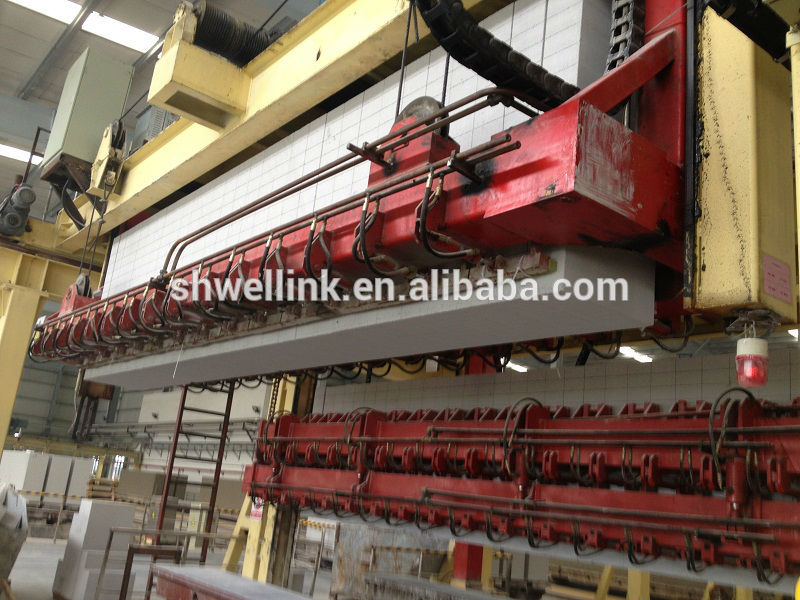
Lower Price High Quality AAC Block Production Line :clamping machine Packing Line The packing line is designed for improved efficiency and reduced labor cost. A number of pallets are arranged along the packing line. Each individual AAC panel is lifted by the crane and put down on the pallet. Once the packing operation is started, the pallet together with the AAC panel moves along the packing line.
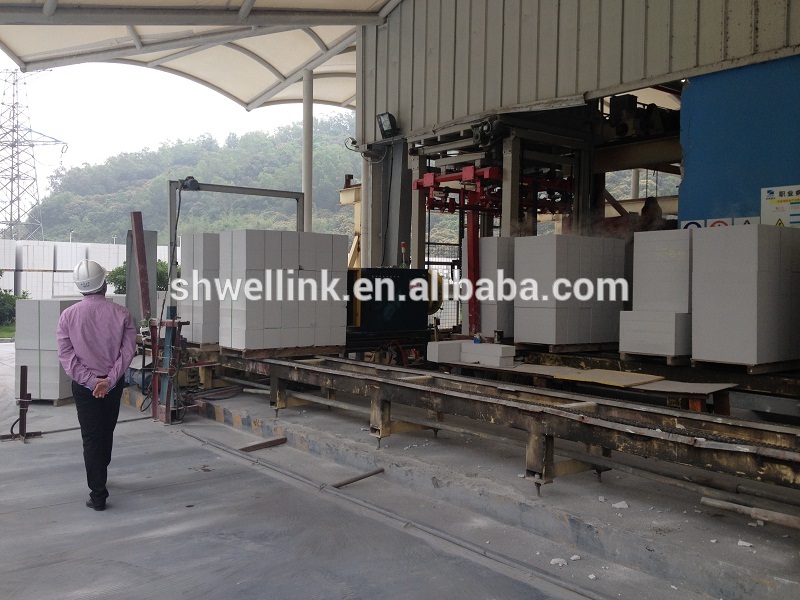
Lower Price High Quality AAC Block Production Line :packing line Annual Output Table
AAC Block Size | 4.2x1.2m | 4.8x1.2m | 5x1.2m | 5x1.5m | 6x1.2m | 6x1.5m |
Annual Output | 150,000m3 | 200,000m3 | 250,000m3 | 300,000m3 | 300,000m3 | 350,000m3 |
Mould Size | 4.2x1.2m | 4.8x1.2m | 5x1.2m | 5x1.5m | 6x1.2m | 6x1.5m |
Number Operators | 10 | 10 | 10 | 10 | 10 | 10 |
With decades of experience in serving the AAC blocks production machinery industry, we can supply customers with quality AAC block production lines with capacity ranging from 150,000m3 to 400,000m3 per year. Packaging & Shipping Packaging Detail: Standard Export Packing Delivery Detail: 90 days after received the 30% prepayment Our Services Our Factory supply best training and after-sales service. Company Information SINOPOWER INDUSTRIAL GROUP is one of professional manufactures about Building Material Machinery more than 15 years, we are the earliest supplier and leader in China. Our advantage is that we have several excellent design professors, high-level engineers and professional machinery process center. Our main products are AAC Brick/Block/Panel Production Line.Fiber Cement Board Production Line so on. Till now we have exported our lines to Russia, Romania, Turkey, Greece, Ukraine, Iran, Pakistan, India and also Indonesia. The products we manufactured belongs to new and high technology industries. We have the advanced enterprise technology center, have a complete technical equipment production base, plant distribution around the country. Business Type: Manufacturer, Trading Company
Main Products: AAC Brick/Block/Panel Production Line.Fiber Cement Board Production Line
Location: Shanghai, China (Mainland)
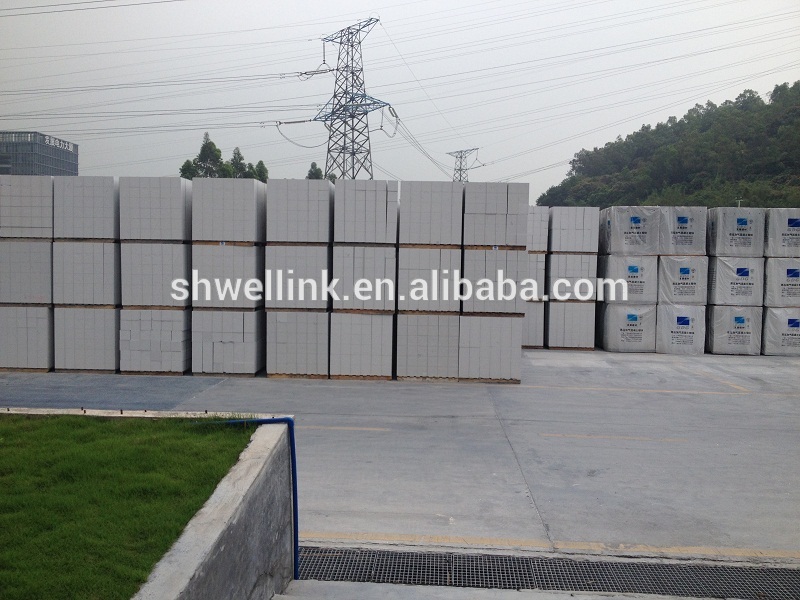
Welcome to visit our factory and China Best AAC Block Panel Making Machinery Manufacturer working site.