Plywood hot press Plywood production line Plywood machinery Complete plywood production line consist of rotary peeling machine, veneer dryer, glue spreader, glue mixer, plywood forming machine, cold press, hot press, automatic edge saw, sanding machine, oil boiler, knife grinder, glue making machine, etc. The following is Processing technology of plywood production line: In the producing process, log cutting, peeling, dry, handling, hot press, edge trimming, sanding affect the wastage. The wastage is remains of processing (materiality) and shrinking (immateriality). Wood wastage is related to the material, specification of log, equipment capability, technology and production specification. 1) Log cutting: Usually import log length is more than 6 meters. Cutting according to the technology required length and quality. The cutting length should be product length add remains. For example, product is 1220mm*2440mm, cutting length usually be 2600mm or 1300mm. log length, camber and demerit affect plywood output directly. Remains are small wood pieces, truncations, sawdust, tec. Log cutting wastage ratio is 3%-10%. 2) Veneer peeling: Peeling is the most popular plywood producing process. Back veneer thickness is about 0.6mm, core veneer and centre veneer thickness is about 1.8mm. 3) Drying: Veneer is moist. it should b e dried according to the technology requirement. After drying, it will shrink. Dimension will become smaller. Veneer length, width, thickness will shrink. Shrink wastage is related to wood material, moisture containing, veneer thickness. Shrink wastage is 4%-10%. 4) Veneer handling: Handling include cutting, putting veneer together and mending. Cut zonal veneer into specification veneer or proper size which can be put together. Narrow zonal veneer can be put together into one veneer. Veneer with demerit can be mended to be qualified. Wastage in this part related to log material, peeled veneer quality, dried quality, and worker operation skill. Wastage ratio is 4%-16%. Import veneer processing plywood wastage ratio is 2%-11%. 5) Hot press: Veneer be glued and stacked , then glue together under set temperature and pressure by hot press. As veneer temperature and moisture containing changes, veneer will shrink. Shrink wastage is related to temperature, pressure, hot press time, wood material, moisture containing, wastage ratio is 3%-8% 6) Edge trimming: Trimming the edge of the plywood flank from hot press to qualified plywood board. Remains related to process remains and product dimension. Production is bigger, wastage is smaller. Wastage ratio is 6%-9% 7) Sanding: Sanding plywood surface to make it good. Wastage is powder. Veneer quality is good, sanding is less. Wastage ratio is 2%-6% 8) Warehousing: Plywood is packing in palletize or in bulk The following are main machinery pictures:
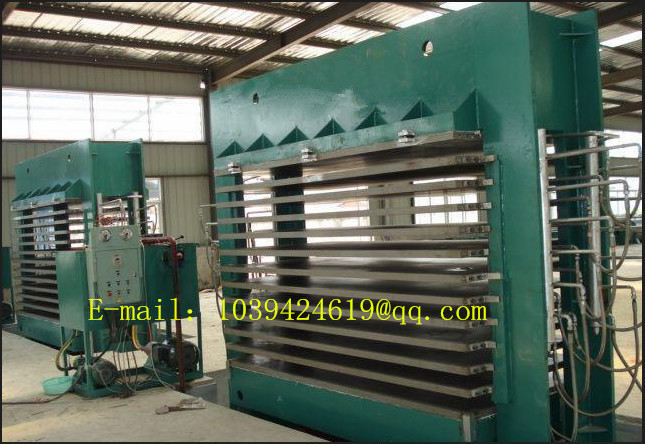
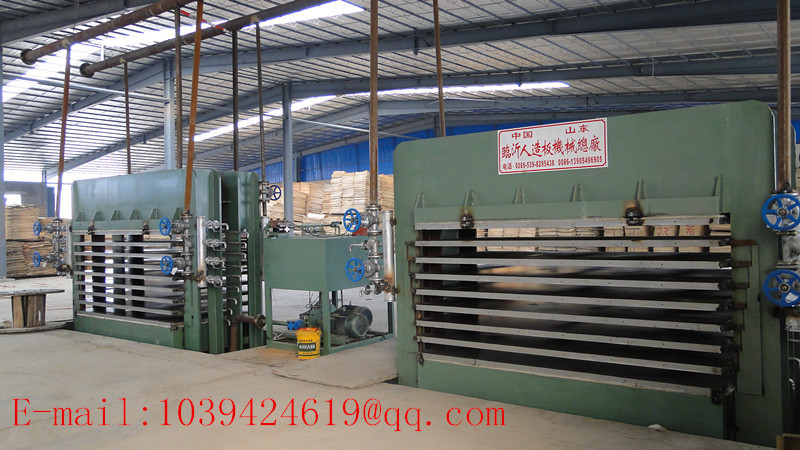
